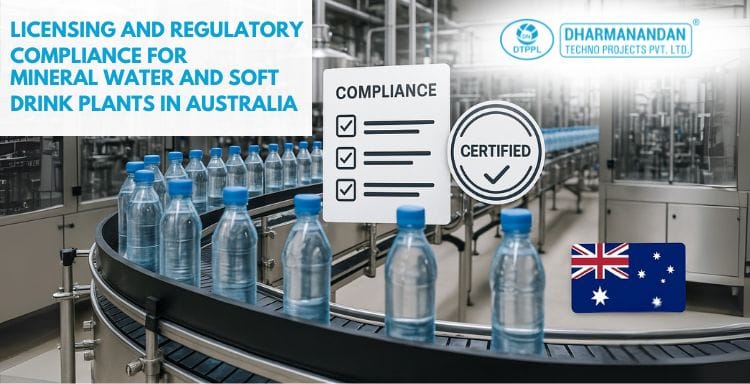
Table of Contents
Mineral Water & Soft Drink Plants in Australia – Licensing & Regulatory Compliance Guide
June 25, 2025
Australia’s beverage manufacturing sector offers considerable opportunities, particularly in the bottled water and soft drinks segments. With a growing preference for packaged hydration and refreshment options, setting up a natural mineral water plant or a soft drinks plant can be a strategic business move. However, the Australian regulatory landscape is detailed and must be navigated with precision.
This how-to guide outlines the step-by-step process to obtain the necessary licenses and meet the mandatory compliance standards for establishing and operating a mineral water factory or soft drinks manufacturing unit in Australia. Whether you plan to launch in Sydney, Brisbane, Melbourne or any regional area, understanding national and local regulations is critical to success.
Step 1: Choose a Suitable Location
Location Considerations:
- Ensure zoning permits manufacturing operations.
- Access to potable water sources is essential for a new mineral water plant.
- Locations near distribution networks may benefit logistics.
You may also assess the feasibility of utilities, especially power and wastewater management, when installing mineral water filling machines and soft drinks processing equipment.
Step 2: Obtain Local Council Approvals and Development Permits
Your proposed facility, whether a soft drink plant or mineral water factory, must secure planning permission from the local council. Applications typically require:
- Site plans showing workflow and waste management.
- Description of intended operations, including filling and packaging.
- Details of machine such as soft drinks filling machines or purification units.
Local councils assess environmental impact, noise and waste generation. Failure to secure development approval may halt the entire project, so early consultation is advised.
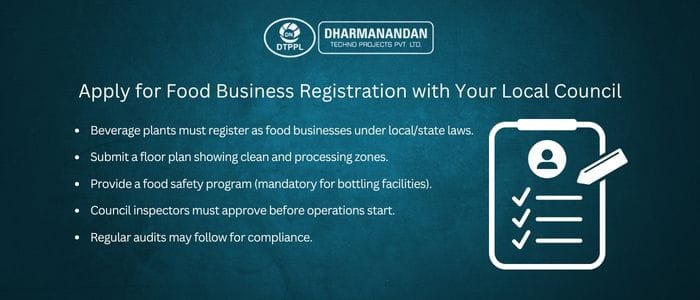
Step 3: Apply for Food Business Registration with Your Local Council
Operating a beverage plant is considered a food business under the Food Act (or respective state legislation). Each council in cities requires businesses to:
- Register the premises as a food manufacturing site.
- Provide a detailed floor plan highlighting clean zones and process areas.
- Submit a food safety program, especially for facilities using Beverages production plants or bottling machines.
Inspectors verify compliance before operations can legally begin. In some cases, periodic audits follow the initial approval to ensure continued adherence to standards.
Step 4: Comply with Food Standards Requirements
FSANZ develops and administers the Australia New Zealand Food Standards Code, which is legally enforceable. Mineral water and soft drinks must comply with the:
Labeling Must Include:
- Ingredient list.
- Date marking.
- Name and address of the business.
- Nutrition information panel.
Failure to meet FSANZ requirements can result in penalties or product recalls. Integrating compliant labeling software into the production workflow can help manage this seamlessly.
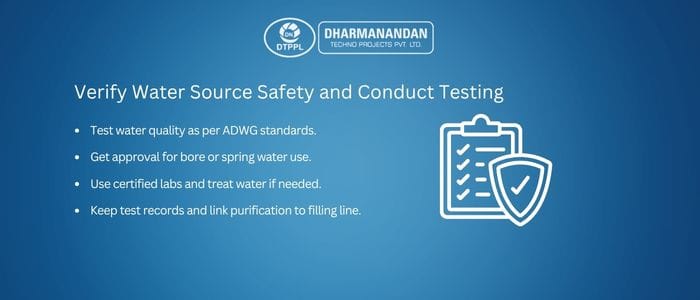
Step 5: Verify Water Source Safety and Conduct Testing
In the case of a natural mineral water plant, source validation is essential. You must test water for microbiological, chemical and physical properties according to Australian Drinking Water Guidelines (ADWG).
Steps for Source Approval:
- Obtain permission for water extraction if using bore or spring sources.
- Conduct laboratory testing at accredited facilities.
- Implement treatment systems if raw water fails purity checks.
Water quality results must be documented and retained for verification during inspections. The purification line should be integrated with the mineral water filling machine to ensure end-to-end product integrity.
Step 6: Install Food-Grade Machinery and Ensure Sanitation Protocols
Machinery used in the facility must be food-grade and compliant with hygienic design standards. The equipment, such as soft drinks filling machines or mineral water bottling lines, should allow:
- Easy cleaning and sanitation.
- Resistance to chemical corrosion.
- Closed-system operations to avoid contamination.
Adopting a documented HACCP system helps in regulatory audits and ensures operational safety.

Step 7: Manage Environmental Regulations and Waste Disposal
Beverage manufacturing involves wastewater, packaging materials and by-products that must be managed under environmental legislation. Requirements include:
- Trade waste approval from your local water authority.
- Waste minimization plans.
- Proper storage and disposal of chemicals.
Efficient operations using modern soft drink production lines or mineral water machines can reduce water usage and waste output. Sustainability is not only recommended – it is often required to secure operating licenses.
Step 8: Prepare for Routine Inspections and Compliance Updates
Once operational, your facility will be subject to periodic inspections by:
- Local council environmental health officers.
- State food safety authorities.
- EPA (if applicable) for waste or emissions management.
Maintain records of:
- Staff training.
- Cleaning schedules.
- Water quality tests.
- Maintenance logs of equipment like soft drinks filling machines.
Continual compliance requires ongoing education, updates to procedures and readiness for audits.
Conclusion
From business registration and facility approval to machinery hygiene and environmental responsibility, the process spans multiple levels of government and compliance domains. Whether starting in Queensland, Victoria or Western Australia, a clear, step-by-step approach ensures legal operation and growth. Facilities equipped with certified systems and technologies, DTPPL offers mineral water filling machines and automated bottling lines, stand to benefit from streamlined workflows and quality consistency.