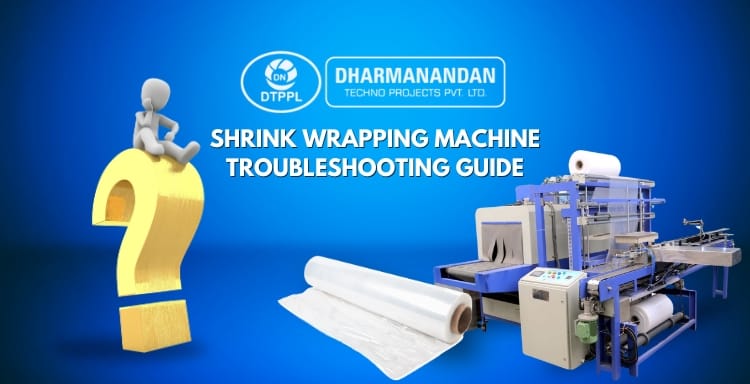
Fully Automatic Shrink Wrapping Machine Troubleshooting: A Complete Guide
April 18, 2025
A Fully Auto Shrink Wrapping Machine is a pivotal piece of equipment in various industries, providing the final touch of packaging to countless products. From bottled water to consumer goods, these machines ensure products are securely wrapped and protected during transportation and storage. However, as with any complex system, issues can arise. Whether you’re dealing with inconsistent shrinkage, film jams, or faulty seals, troubleshooting these problems efficiently is crucial to maintaining production flow and product quality.
In this article, we will explore common issues with Automatic Shrink Wrapping Machines, their causes, and practical solutions to help keep your equipment running smoothly. Whether you’re using a Semi Auto Shrink Wrapping Machine or a fully automated model, this guide will help you tackle and resolve common challenges, ensuring your packaging line operates without interruptions.

Common Problems with Shrink Wrapping Machines and Solutions
1. Uneven Shrinking
One of the most common issues faced with shrink wrap machines is uneven shrinking. This can result in loose areas, dog ears, or wrinkles, which are often visible on the final packaged product.
Possible Causes:
- Inconsistent Tunnel Temperature: If the heat inside the shrink tunnel is uneven, it can cause uneven shrinking of the film.
- Incorrect Conveyor Speed: If the product moves too fast, the film may not shrink properly. Conversely, if the conveyor moves too slowly, the film may overheat and distort.
- Improper Airflow: Uneven airflow in the tunnel can create hot spots or cold spots, leading to inconsistent shrinkage.
- Incorrect Film Tension: Too much or too little tension on the film can prevent it from shrinking evenly.
- Film Quality Issues: Variations in film thickness or quality can lead to uneven results.
Troubleshooting Steps:
- Check Tunnel Temperature: Measure the temperature at multiple points within the tunnel to identify any variations. Use an infrared thermometer for accuracy.
- Verify Conveyor Speed: Refer to the machine’s manual for the recommended speed settings. Adjust the speed using a tachometer if necessary.
- Inspect Airflow: Ensure that air circulation fans and vents are unobstructed and functioning correctly. Clean any clogged filters.
- Adjust Film Tension: Consult the machine’s manual for proper tension settings. Make small adjustments to improve the shrinkage consistency.
- Check Film Quality: Inspect the film for defects like wrinkles, creases, or inconsistencies. Contact your supplier if you suspect a film quality issue.
Key Insight: Uneven shrinking is often caused by variations in temperature, airflow, or film tension. Always adjust these parameters before concluding that the film quality is the issue.
2. Film Jams or Breaks
Film jams or breaks during the shrink wrapping process can disrupt the entire packaging line, leading to significant downtime.
Possible Causes:
- Excessive Film Tension: Too much tension can cause the film to tear or break.
- Worn or Damaged Rollers: If the rollers are worn or damaged, they may snag or tear the film.
- Improper Film Threading: Incorrect threading can cause the film to bind or tear.
- Sharp Edges on Machine: Sharp edges or burrs on machine components can cut the film.
- Static Electricity: Static can cause the film to cling to machine parts, leading to jams.
- Film Roll Defects: Defective film rolls with creases, tears, or uneven winding can cause problems.
- Incorrect Film Type: Using the wrong type of film for the machine can lead to jams.
Troubleshooting Steps:
- Reduce Film Tension: Adjust the unwind tension based on the machine’s manual. Gradually decrease the tension to prevent tearing.
- Inspect Rollers and Guides: Look for wear or contamination on the rollers. Clean or replace any damaged parts.
- Re-Thread Film: Ensure that the film is threaded correctly through the machine. Follow the correct path as outlined in the manual.
- Check for Sharp Edges: Power off the machine and inspect it for sharp edges or burrs. Smooth any rough edges with fine tools.
- Control Static Electricity: Ensure the machine is grounded, and consider using anti-static devices if static buildup is a concern.
- Inspect Film Roll: Look for defects like creases or uneven winding. If the film appears faulty, contact the supplier for a replacement.
Key Insight: Film jams are often caused by excessive tension, obstructions, or sharp edges. Regular maintenance of rollers and proper film handling can prevent these issues.
3. Sealing Problems (Weak or Incomplete Seals)
A poor or incomplete seal is one of the most common and frustrating issues with Automatic Shrink Wrapping & Packaging Machines. Weak or incomplete seals compromise the integrity of the package, leading to damage or contamination of the product.
Possible Causes:
- Incorrect Sealing Temperature: If the sealing bar is too cold, the film won’t seal properly. If it’s too hot, the film can burn or melt excessively.
- Insufficient Sealing Time: If the film doesn’t spend enough time in contact with the sealing bar, the seal may be weak.
- Worn or Damaged Sealing Bar/Wire: Over time, sealing bars can wear down, preventing a consistent seal.
- Improper Sealing Pressure: Insufficient pressure can lead to weak seals, while excessive pressure can damage the film or the machine.
- Film Incompatibility: The film may not be compatible with the sealing temperature or method.
- Contamination on Sealing Surfaces: Film residue or dirt on the sealing surfaces can prevent proper sealing.
Troubleshooting Steps:
- Verify Sealing Temperature: Use a thermometer to check the temperature of the sealing bar. Adjust it based on the recommended settings in the machine’s manual.
- Check Sealing Time: Refer to the manual for the recommended sealing time and adjust accordingly.
- Inspect Sealing Bar/Wire: Power off the machine and examine the sealing bar for wear or damage. Clean the sealing surfaces regularly to prevent contamination.
- Check Sealing Pressure: Adjust the pressure settings as per the manufacturer’s guidelines.
- Verify Film Compatibility: Ensure the film type is compatible with the sealing method and temperature used.
Key Insight: Sealing problems are usually related to temperature, time, pressure, or the condition of the sealing surface. Always address these factors to ensure a strong, consistent seal.

Predictive Shrink Wrapping Machine Troubleshooting: Staying Ahead of the Game
Effective troubleshooting isn’t just about solving problems as they arise; it’s about preventing them before they happen. By incorporating predictive maintenance techniques into your shrink wrapping operation, you can identify issues early and avoid costly downtime.
1. Data Logging and Trending
Monitor key operating parameters such as temperature, pressure, and speed to detect any deviations from normal operation. Analyzing trends helps predict future problems and provides insights into potential failures.
2. Regular Inspections
Thorough inspections are crucial. Use a flashlight and magnifying glass to check for wear and tear on machine components that may not be immediately visible during routine checks.
3. Component Lifespan Tracking
Track the operating hours or cycles of critical components like sealing bars, rollers, and motors. By replacing components proactively, you can avoid unexpected failures and maintain machine performance.
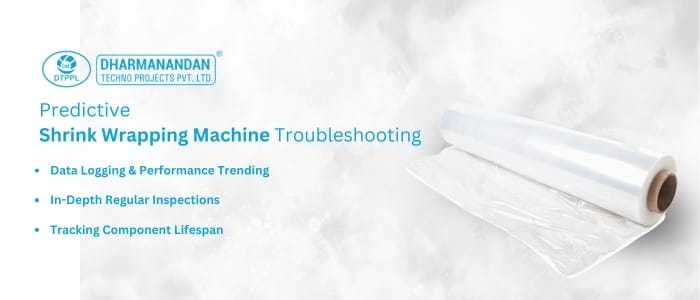

Conclusion: Troubleshooting Your Shrink Wrapping Machine with Confidence
When troubleshooting a Semi Automatic Shrink Wrapping Machine or Fully Auto Shrink Wrapping Machine, understanding the root cause of each issue is key to finding a solution. Whether it’s adjusting temperature settings, addressing film jams, or ensuring proper sealing, taking a methodical and informed approach will help minimize downtime and keep your production line running smoothly.
At DTPPL, we are proud to be a leading Automatic Shrink Wrapping Machine Manufacturer. With our expertise in providing shrink wrapping machines for various industries, we understand the challenges faced by plant operators. That’s why we’re committed to offering reliable equipment and providing troubleshooting tips to ensure your shrink wrap machines are always in optimal condition.
DTPPL Is Here For You
For the best Semi Automatic Shrink Wrapping Machines and Fully Auto Shrink Wrapping Machines, trust DTPPL. As an experienced Automatic Shrink Wrapping Machine Supplier and Exporters, we offer high-quality machines that meet the demands of your production line. Contact us today to learn more about our products and get expert advice on machine setup and maintenance!