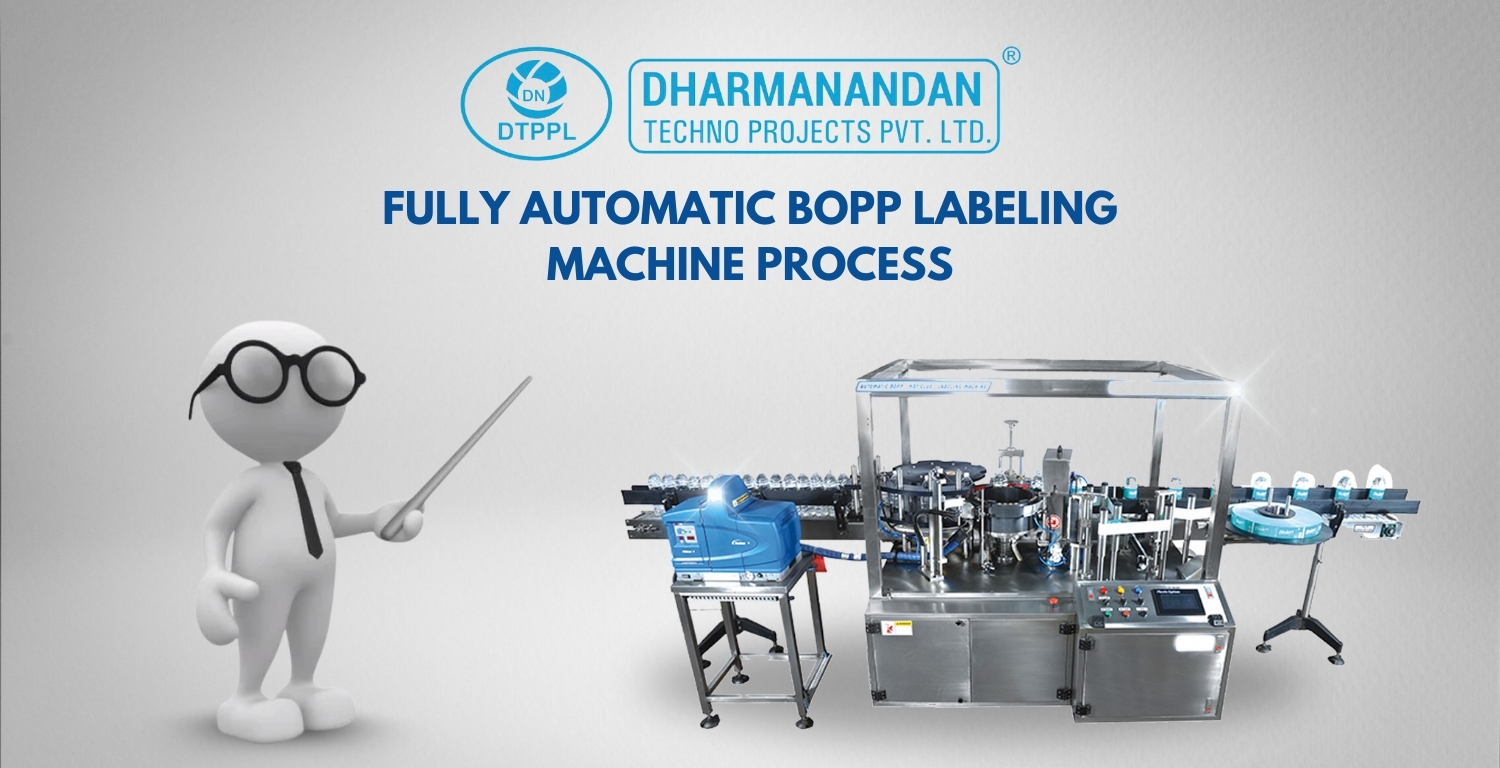
Table of Contents
The Process of Fully Automatic BOPP Labeling Machine
February 14, 2025
In the world of modern packaging, efficiency and precision are crucial. The BOPP Labelling Machine plays a significant role in ensuring high-quality labeling for products, particularly in mineral water/packaged drinking water plants. This article explores the in-depth process of Fully Automatic BOPP Labeling Machines, their components, working mechanism, and benefits.
Understanding BOPP Labels
Biaxially Oriented Polypropylene (BOPP) is a plastic film widely used in the labeling industry due to its durability, clarity, and moisture resistance. BOPP Labeling Machine technology ensures that labels adhere seamlessly to containers, providing a professional and long-lasting finish. These machines utilize roll-fed technology, enhancing efficiency and reducing label wastage.
BOPP labels are designed to withstand moisture, temperature variations, and mechanical wear, making them ideal for bottled water packaging. The Automatic BOPP Labeling Machine ensures high-speed application with minimal errors, maintaining brand consistency and product appeal.
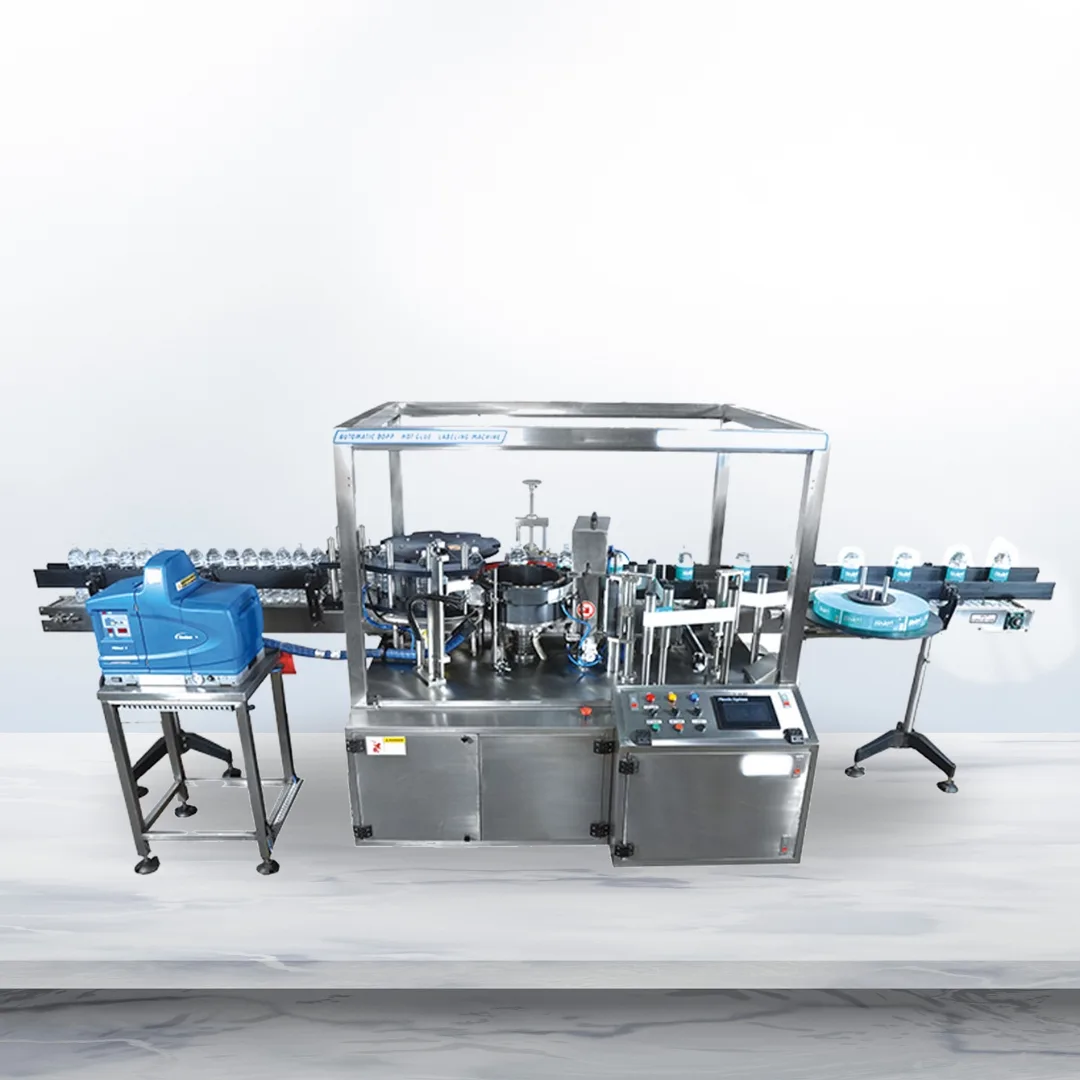
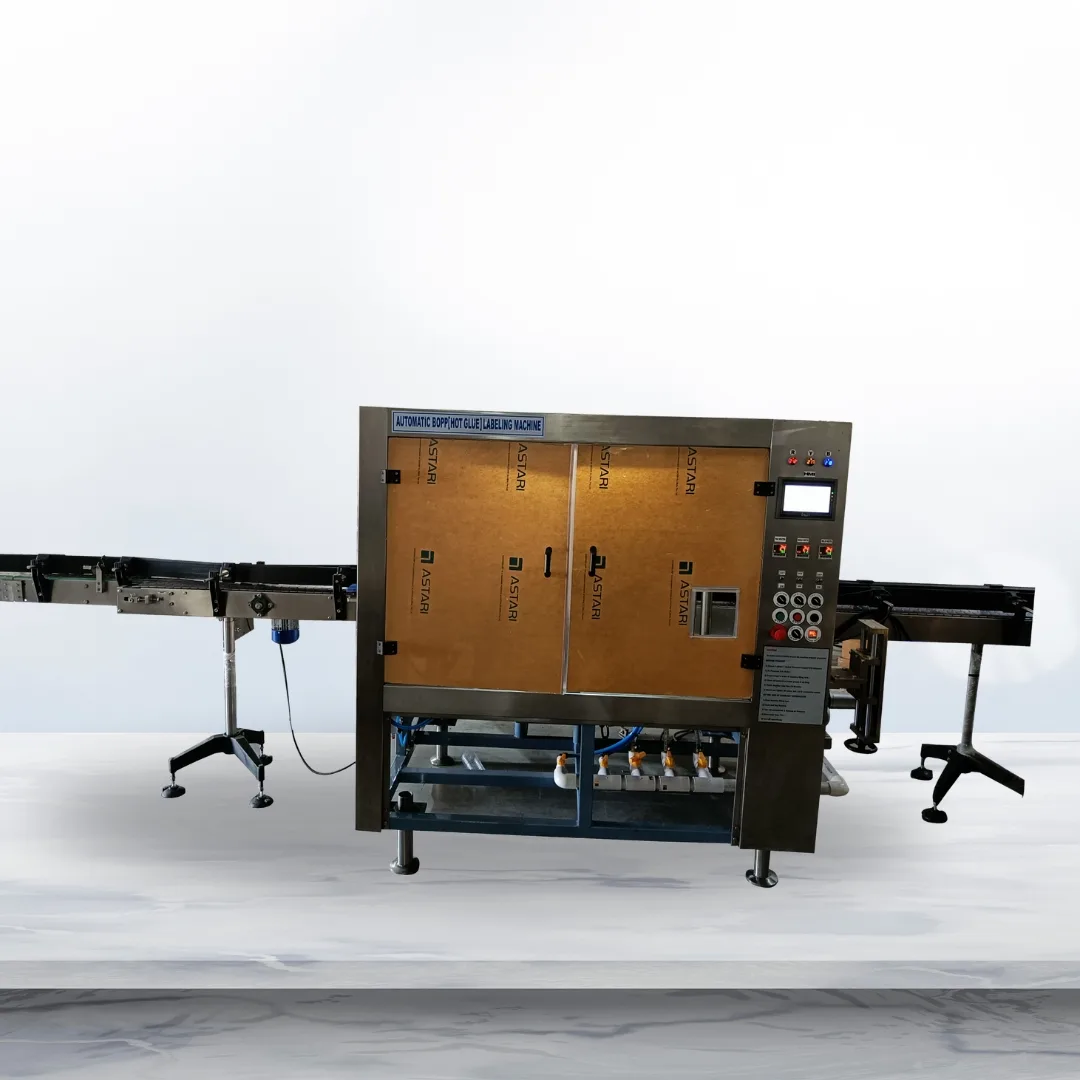
Working Process of the Automatic BOPP Labeling Machine
The labeling process in an Automatic BOPP Labeling Machine follows a systematic and automated sequence, ensuring precision and consistency. Below is a breakdown of the steps involved:
1. Label Unwinding
- A roll of BOPP labels is loaded onto the unwind unit.
- The tension control system ensures smooth unwinding of the film without distortion.
2. Printing and Registration Control
- If the roll-fed labels require additional details like batch codes or expiry dates, an integrated printing system is used.
- Sensors ensure proper registration of labels to maintain perfect alignment.
- Optical sensors detect pre-printed marks on the film for precise label positioning.
3. Cutting Mechanism
- The continuous roll of labels is cut into individual labels using precision rotary or laser cutting systems.
- BOPP Labeling Machine ensures that each cut is sharp, avoiding jagged edges or uneven shapes.
Cut and Stack vs. Roll-Fed:
- Cut and Stack: Labels are pre-cut and stacked before being fed into the machine.
- Roll-Fed: A continuous roll is cut on-demand, improving efficiency.
4. Adhesive Application
The machine applies adhesive using one of the following methods:
- Hot Melt Glue: A thermoplastic adhesive that melts at high temperatures and solidifies upon application.
- Cold Glue: Water-based adhesive suitable for certain labeling needs.
- Heat-Activated Glue: Utilizes pre-applied adhesive that bonds upon heat exposure.
Advantages of Hot Melt Glue:
- Instant bonding, reducing downtime.
- Strong adhesion even in humid environments.
- Reduces label waste and improves cost-effectiveness.
5. Label Application
- The cut label is positioned accurately and applied to the container.
- A wrap-around mechanism ensures that the label adheres smoothly without wrinkles or bubbles.
- The speed and precision of Automatic BOPP Labeling Machines make them ideal for high-speed production lines in a Packaged Drinking Water plant.
6. Post-Application Pressing and Finishing
- The labeled bottles pass through rollers or brushes to ensure firm adhesion.
- Quality inspection is conducted using automated vision systems to detect misalignment or defects.
- Non-compliant bottles are automatically rejected, ensuring only high-quality labeled products proceed.
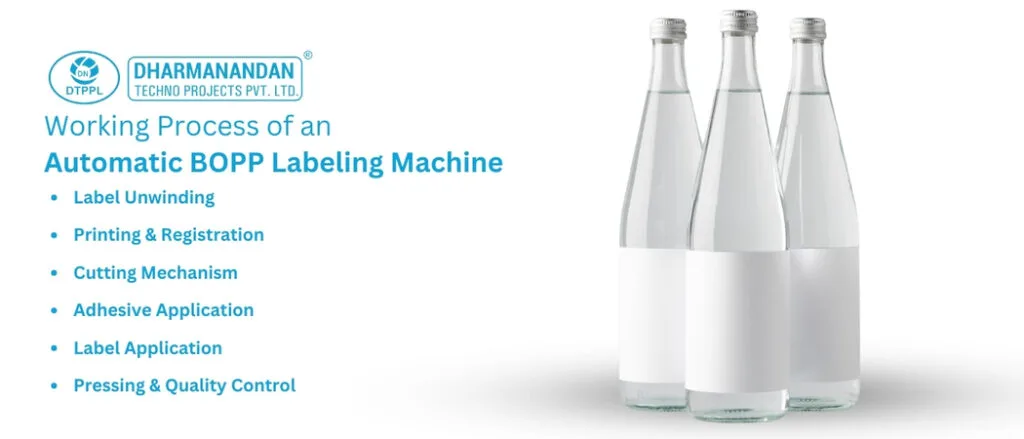
Key Components of a BOPP Labelling Machine
- Label Unwind Unit – Holds and feeds the roll of labels.
- Tension Control System – Prevents slack and ensures proper film tension.
- Cutting Unit – Precisely cuts labels from the roll.
- Glue Application System – Ensures even distribution of adhesive.
- Label Application Unit – Positions and applies the label on containers.
- Conveyor System – Moves products seamlessly through the labeling process.
- PLC & HMI System – Controls the entire machine operation and provides an interactive user interface.
- Product Handling System – Uses conveyors, timing screws, and positioning guides to ensure accurate placement of bottles.
Advantages of BOPP Labeling Technology
- High-Speed Operation: Fully automated, allowing high production efficiency.
- Durability: BOPP labels are water-resistant, scratch-proof, and tear-resistant.
- Cost-Effectiveness: Reduces material waste and speeds up packaging.
- Aesthetic Appeal: Provides a seamless finish with vibrant, high-gloss designs.
- Eco-Friendly: Recyclable material, contributing to sustainability.
- Low Maintenance: With advanced automation, BOPP Labeling Machines require minimal manual intervention, reducing operational costs.
- Flexibility: Can label various bottle shapes and sizes, making it suitable for diverse production lines.
BOPP Labeling Machine Price Considerations
The BOPP labeling machine price varies depending on factors such as:
- Machine speed and automation level.
- Integration with other packaging equipment.
- Customization options (e.g., multi-layer labeling, special adhesives, etc.).
- Brand and technical support availability.
- Additional features like automatic error detection, multiple label types, and energy-efficient operations.
Investing in a BOPP Labeling Machine can significantly enhance production efficiency and branding appeal while reducing long-term costs.
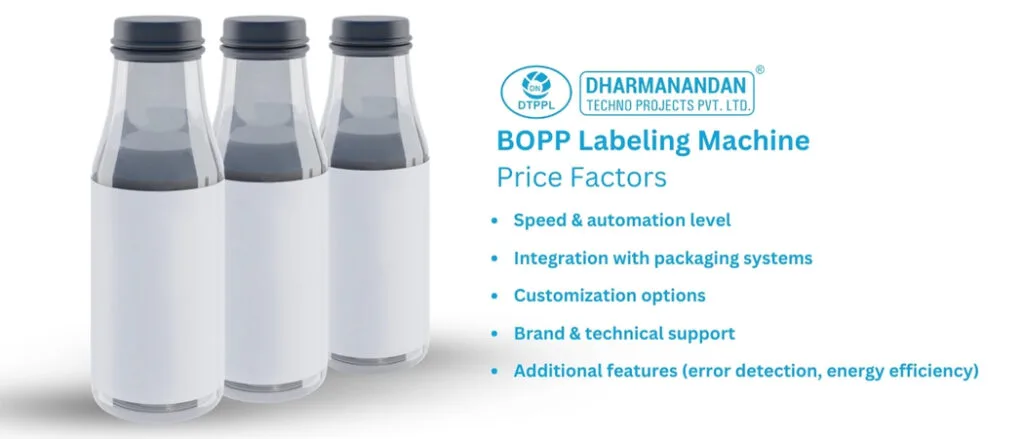

Conclusion
A Fully Automatic BOPP Labelling Machine is an indispensable asset for the Packaged Drinking Water and Packaged Natural Mineral Water industries. By combining speed, efficiency, and durability, these machines ensure high-quality labeling with minimal errors.
With technological advancements such as AI-based vision control, Industry 4.0 integration, and hybrid adhesive technologies, the future of BOPP Labeling Machines is promising. Businesses looking for reliable and cost-effective labeling solutions should consider adopting this advanced technology to stay ahead in the competitive packaging industry.