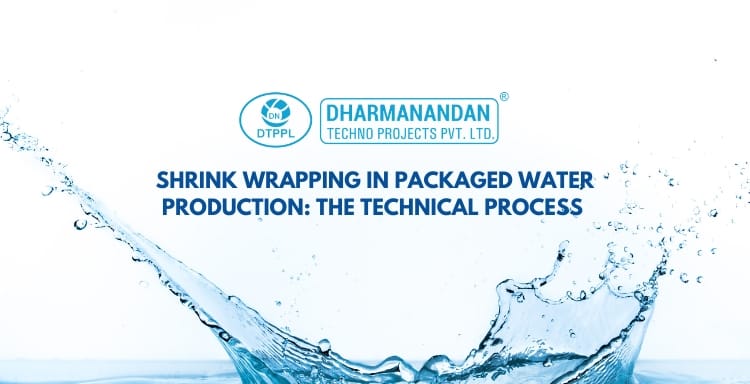
Table of Contents
Shrink Wrapping in Packaged Water Production: The Technical Process
February 11, 2025
In modern packaged water production, shrink wrapping is not just about protecting a product – it’s about presenting it with quality and care. Fully automatic shrink wrapping machines transform loose assemblies into tightly sealed, tamper-evident packages that are both protective and visually appealing. This article provides an efficient overview of how these machines work, covering key wrapping methods, shrink film science, heating and sealing systems and the advanced automation behind them.
1. The Fully Automatic Shrink Wrapping Machine: The Master of the Snug Fit
Fully automatic shrink wrapping machines integrate into high-speed production lines in a protective layer of shrink film. Engineered for efficiency and precision, these machines ensure that every item is securely wrapped and attractively presented with minimal human intervention. Manufacturers looking to export quality packaging often turn to an Automatic Shrink Wrapping Machine Exporter for reliable solutions.
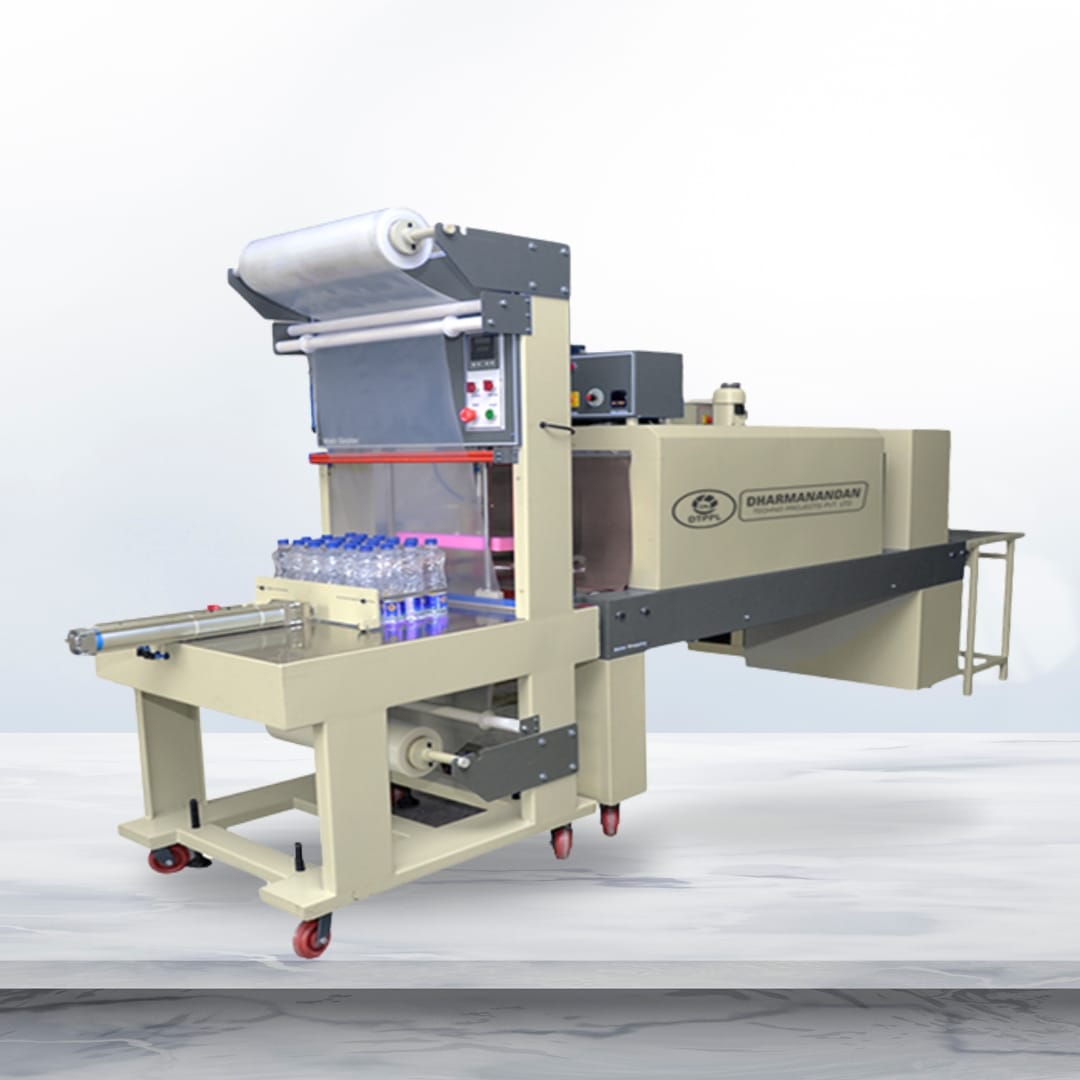
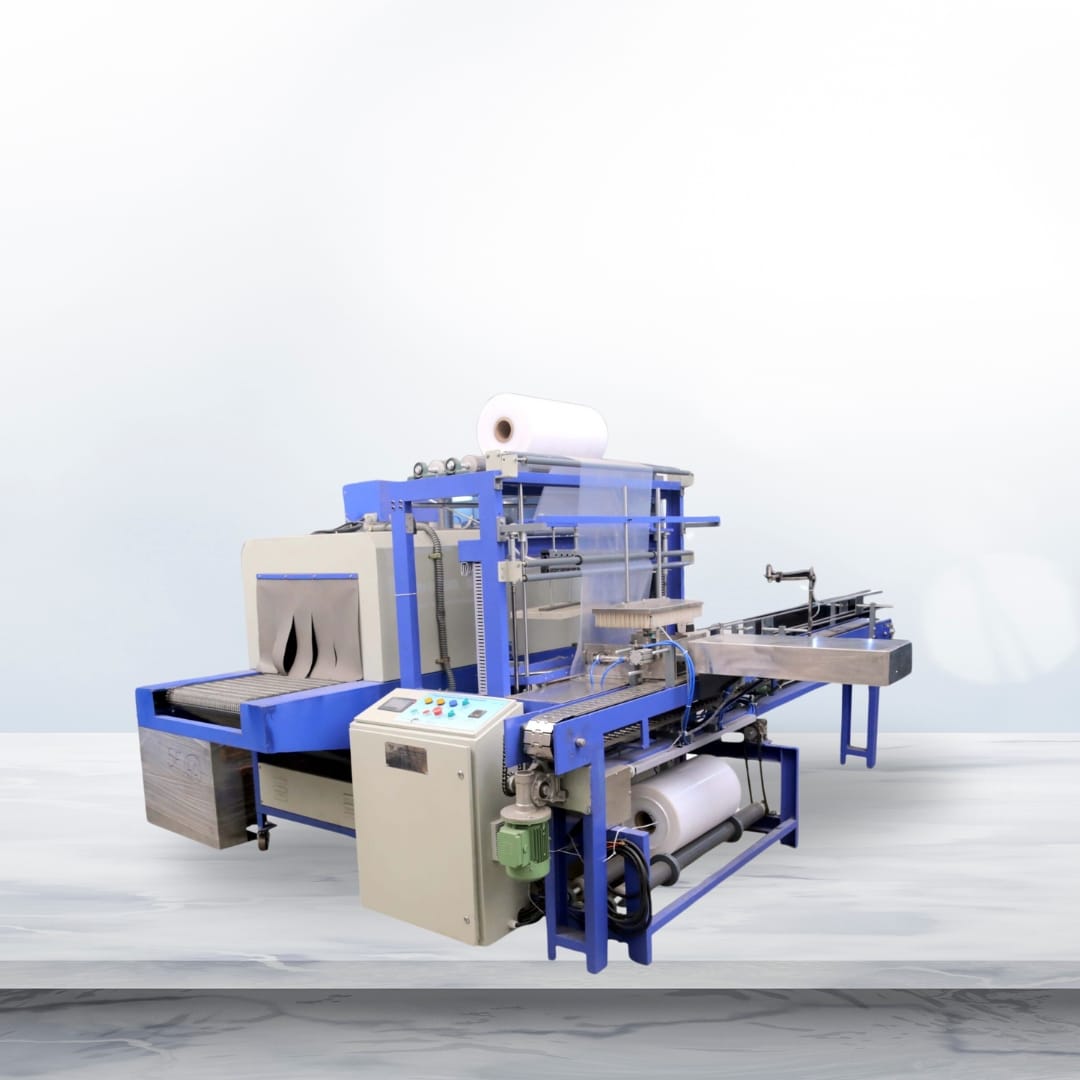
2. Choosing the Right Automatic Shrink Wrapping Method for Packaged Water Production
The wrapping method depends on the product’s shape, size, desired appearance, production speed and budget. Here are the primary methods:
a) L-Bar Sealing
- Principle: The product is wrapped in film and sealed along two open edges using an L-shaped heated bar.
- Process:
- The product is positioned on a conveyor or infeed table.
- Shrink film is dispensed from a roll and wrapped around the product.
- An L-shaped heated sealing bar descends to simultaneously seal the two open edges of the film, forming a bag-like enclosure.
- Pros & Cons:
Pros: Versatile and cost-effective and suitable for wide range of products.
Cons: May leave a small “bullseye” opening and also not ideal for very high speeds. - Modern L-Bar sealers reduce the ‘bullseye opening’ by using perforated seals or reinforced shrink bands. Advanced machines integrate micro-perforation techniques to improve breathability while maintaining package integrity.
b) Side Sealing
- Principle: The product is continuously wrapped, with overlapping film edges along the side sealed by a heated wheel.
- Process:
- The product is fed along a conveyor.
- Film is dispensed and folded around the product as it moves.
- The product, now encased in a tube of film, is conveyed into a heat tunnel to complete the shrink process.
- Pros & Cons:
Pros: Supports higher speeds and creates a seamless seal.
Cons: Requires precise synchronization between film dispensing and product movement. - To maintain precise film tension, modern side sealers use servo-driven rollers that adjust film feed rate dynamically. These machines also employ edge-guided sealing wheels with Teflon coatings to prevent sticking and ensure seamless sealing at high speeds.
c) Overlap Sealing (Flow Wrapping)
- Principle: Film is formed into a tube around the product with an overlapping “fin” sealed by heated rollers.
- Process:
- Products are fed onto a conveyor with carefully controlled spacing.
- Film is dispensed from a roll and formed into a continuous tube around the product flow.
- A pair of heated rollers or sealing jaws create a longitudinal seal along the area where the film overlaps.
- A cutting mechanism then produces cross seals, dividing the continuous film into individual packages.
- Pros & Cons:
Pros: High speed and efficient for multipacks.
Cons: Not suitable for all product shapes; the fin seal may not always be ideal. - Adjustable sealing pressure and temperature control ensure that the film is sealed effectively without overheating. High-performance flow wrappers use Teflon-coated sealing jaws to prevent film buildup and optimize fin seal strength.
d) Sleeve Wrapping
- Principle: A band or sleeve of film is formed around the product, leaving the ends open.
- Process:
- The product is conveyed along the production line.
- Film is dispensed and formed into a sleeve around the product.
- The overlapping edges are sealed either by applying heat or using an adhesive.
- The product may then proceed through a heat tunnel to shrink the sleeve snugly around.
- Pros & Cons:
Pros: Excellent for bundling and creating tamper-evident seals.
Cons: Does not provide full enclosure. - To enhance efficiency, advanced sleeve wrapping machines adjust heat tunnel parameters automatically based on sleeve material properties, ensuring optimal shrinkage without distorting the product shape
Each method can be found in various solutions, such as a Semi Automatic Shrink Wrapping Machine designed for smaller-scale operations. For larger scale production, companies might invest in a Fully Auto Shrink Wrapping Machine for continuous high-speed packaging.
3. The Science of Shrink Wrapping Film Machine in Water Packaging Plant
Shrink films are engineered to contract when heated, conforming tightly to the product. Key types include:
- Polyolefin:
Features multi-layer construction, a high shrink percentage and biaxial orientation for uniform shrinkage. POF is popular for its clarity and strength.
Key Features:
- Multi-Layer Construction: POF films are often composed of several layers, with each layer contributing properties such as enhanced strength, barrier protection and improved sealability.
- High Shrink Percentage: When exposed to heat, POF films shrink significantly, ensuring a tight, conforming wrap around the product.
- Biaxial Orientation: These films are stretched in both the machine direction (MD) and the transverse direction (TD), which imparts strength and ensures uniform shrinkage.
- Modern POF films contain multiple functional layers, including anti-fog, UV protection, and anti-static coatings. These properties help maintain product clarity and prevent dust accumulation on packaging.
- Polyvinyl Chloride (PVC):
Offers high gloss and stiffness, making it suitable where a premium look is needed, despite environmental concerns. - Polyethylene:
Known for heavy-duty applications, PE is thicker and less prone to shrinkage, ideal for pallet wraps and robust sleeves. - While PE is widely used for bundling, newer formulations include low-density variants that offer improved clarity and shrink performance. Manufacturers also use co-extruded PE films to enhance puncture resistance while maintaining flexibility.
Manufacturers may work with Automatic Shrink Wrapping Machine Manufacturer ensure the films meet stringent requirements.
Critical Auto Shrink Wrapping Film Properties
- Shrink Force:
This is the force exerted by the film as it contracts, ensuring a snug fit without damaging the product. - Seal Strength:
The ability of the film to form a strong, durable seal when heated is essential for maintaining package integrity. - Clarity and Gloss:
These aesthetic properties are important for applications where product visibility and shelf appeal are priorities. - Barrier Properties:
The film’s capacity to block moisture, oxygen and other gases is crucial for preserving product quality and extending shelf life. - Puncture and Tear Resistance:
High resistance to punctures and tears ensures that the package remains intact during handling and transportation.
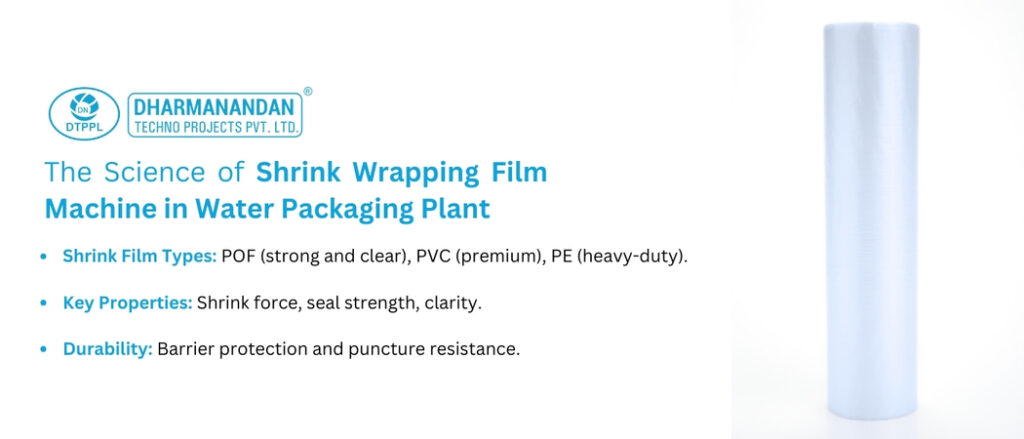
4. Heating and Sealing Systems of Shrink Wrap Machine in Packaging Drinking Water
Heat is essential for both sealing the film and triggering its shrinkage.
Sealing Systems
- Heated Sealing Bar (L-Bar Sealers):
Uses a heated bar, often coated with non-stick materials, to seal film edges. - Heated Sealing Wheel (Side Sealers):
A rotating wheel that continuously seals film along a product’s side. - Hot Air and Impulse Sealing:
Utilize hot air jets or brief heat pulses to create seals, especially useful for thicker films.
Heat Tunnels
Heat tunnels use convection or infrared heating to distribute heat evenly, shrinking the film around the product. Special factors include temperature control, airflow management and dwell time, which is adjusted by the conveyor speed and tunnel length. Compared to convection heating, infrared heat tunnels provide faster and more uniform film shrinkage by directly heating the film surface. This reduces energy consumption and improves package appearance by preventing over-shrinking.
5. Automation and Control of Fully Automatic Shrink Wrapping Machine
Advanced automation ensures precision and efficiency throughout the wrapping process. Key elements include:
- Film Dispensing and Feeding:
Rollers, guides and sensors ensure consistent tension and alignment. - Product Infeed and Spacing:
Conveyor systems, timing screws and guides maintain proper spacing and alignment. - Sealing and Cutting Mechanisms:
Precisely timed actuators coordinate sealing and cutting to create individual packages. High-speed shrink wrapping systems integrate servo-controlled sealing pressure adjustments, ensuring that different film thicknesses receive the optimal force for a strong, tamper-proof seal. - Heat Tunnel Control:
Temperature sensors and control algorithms adjust heat and conveyor speed for uniform shrinkage. - Safety and Control Systems:
Emergency stops, safety interlocks and guards protect operators, while a central PLC and HMI provide real-time monitoring and adjustments.
For businesses seeking reliability and quality, partnering with an Automatic Shrink Wrapping Machine Supplier ensures access to cutting-edge technology. Companies often choose from providers offering solutions like Automatic Shrink Wrapping & Packaging Machine systems.
6. Key Components and Its Functions of Shrink Wrap Machine in Water Packaging Plant
The critical components of a fully automatic shrink wrapping machine sheds light on how these systems achieve such high levels of precision and reliability.
a) Film Unwind and Dispensing Unit
- Film Roll Holder/Spindle:
This component supports the shrink film roll and allows it to unwind smoothly during operation. - Tension Control System:
Employing brakes and dancer arms, this system maintains consistent tension on the film, preventing wrinkles, tears or misfeeds. - Film Tracking System:
Sensors and edge guides ensure that the film remains properly aligned as it travels through the machine, reducing the risk of misalignment.
b) Infeed and Product Handling System
- Conveyor Belts:
These belts transport products at a controlled speed and are selected based on their compatibility with the products being wrapped. - Product Spacing Mechanisms:
Devices such as timing screws or indexing conveyors ensure that products are evenly spaced, facilitating smooth wrapping and preventing collisions. - Product Guides:
It align products accurately as they enter the wrapping zone, ensuring a consistent final package.
c) Sealing System
- Sealing Bar/Jaw:
Equipped with heating elements and non-stick coatings, the sealing bar applies heat and pressure to form a strong, reliable seal. In side sealing applications, a continuously rotating sealing wheel maintains a uniform seal along the product’s edge. - Cutting Mechanism:
Integrated with the sealing system, the cutting separates individual packages from the continuous film.
d) Heat Tunnel
- Heating Elements and Air Circulation:
The heat tunnel houses resistance heaters, infrared elements or gas burners, with fans circulating hot air to ensure uniform film shrinkage. - Insulation and Conveyor System:
Insulation minimizes heat loss and a carefully calibrated conveyor system controls the dwell time of products within the tunnel.
e) Control System and Electronics
- PLC and HMI:
The PLC serves as the central processing unit orchestrating all machine functions, while the HMI offers operators an intuitive interface for monitoring and adjustments. Next-generation shrink wrapping machines are equipped with Industry 4.0 capabilities, including real-time remote monitoring, predictive maintenance using AI, and automated production reporting. These systems integrate with cloud-based data analytics to optimize machine performance and reduce downtime. - Servo/Stepper Motors and Sensors:
These components ensure precise control of film dispensing, product positioning and sealing actions, while sensors monitor critical parameters like film tension and temperature.
7. Applications and Industries of Shrink Wrapping Machines
Fully automatic shrink wrapping machines are used in a wide variety of industries. While they play a crucial role in packaging drinking water and natural mineral water, their applications extend far beyond:
- Fully Automatic Shrink Wrapping Machines Supports Food and Beverage:
Shrink wrapping is commonly used to package food items such as meat trays, produce, baked goods and frozen foods. - Fully Automatic Shrink Wrap Supports Pharmaceuticals:
In the pharmaceutical industry, shrink wrapping provides a tamper-evident and protective barrier for medicine boxes, pill bottles and medical devices, ensuring product integrity and compliance with stringent regulations. - Cosmetics and Personal Care by Shrink Wrapping:
Products such as cosmetics, toiletries and personal care items are shrink wrapped to enhance their visual appeal while ensuring they remain secure during transit. - Print and Publishing by Automatic Shrink Wrapping:
Magazines, books and catalogues are shrink wrapped to protect them during shipping and handling, ensuring they arrive in pristine condition. - Fully A utomatic Shrink Wrapping Machines Industrial and Consumer Goods:
Shrink wrapping is used to package a wide array of items – from hardware and toys to sporting goods and electronics – providing essential protection against dust, moisture and physical damage. - Logistics and Distribution of Shrink Wrapping :
In logistics, shrink wrapping is an indispensable tool for securing loads on pallets, enhancing stability and reducing damage during transportation.
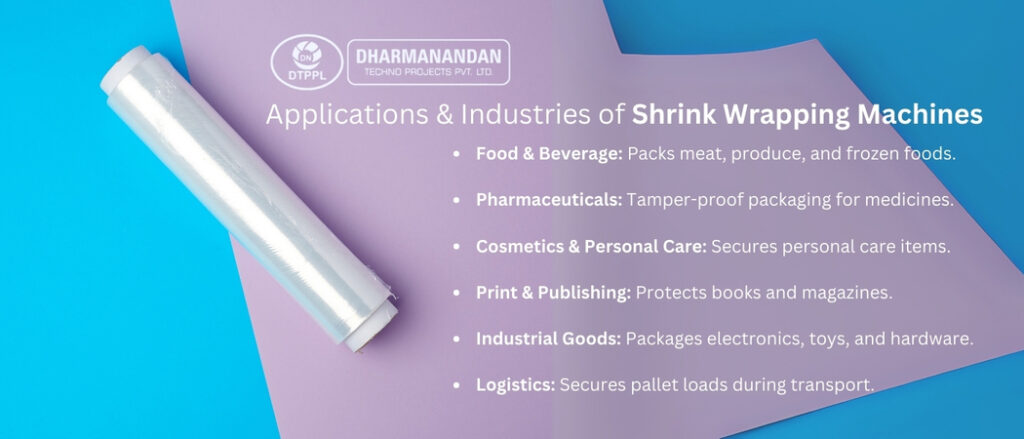
8. Advantages of Fully Automatic Shrink Wrapping Machines:
- Tamper Evidence of Shrink Wrap Machine: Provides a clear indication if a package has been opened or tampered with, enhancing product security and consumer confidence.
- Automatic Shrink Wrapping Enhances Product Presentation: Creates a tight, conforming wrap that can improve the appearance of the product, making it more visually appealing to consumers.
- Bundling and Multipacking of Shrink Wrapping: Facilitates the creation of multipacks or bundles of products, making them easier to handle, display and sell.
- Shrink Wrapping Reduces Packaging Material: Compared to some other packaging methods, shrink wrapping can use less material, contributing to cost savings and reduced environmental impact.
- Shrink Wrap Provides High Speed and Efficiency: Fully automatic machines can wrap products at very high speeds, significantly increasing production output.
9. The Future of Shrink Wrapping in Packaged Natural Mineral Water Plant
Looking ahead, the technology behind shrink wrapping is evolving with trends such as:
- Smart Packaging: Integration of sensors for real-time environmental monitoring and active packaging solutions.
- Industry 4.0 Integration: Enhanced IIoT connectivity for remote monitoring, predictive maintenance and data-driven optimization.
- Enhanced Automation: Robotic integration, vision systems for quality control and AI-driven self-adjusting machines for improved efficiency.

Conclusion
Fully automatic shrink wrapping machines play a vital role in the packaged water industry. They combine advanced technology, precise engineering and innovative materials to protect products and present them attractively. By choosing the right wrapping method, utilizing high-quality shrink films and employing sophisticated heating, sealing and automation systems, manufacturers can ensure every product reaches consumers in pristine condition.
As the industry moves toward smarter, more connected production lines, the future of shrink wrapping looks promising – offering greater efficiency, environmental benefits and superior product quality. These machines truly embody the art and science of modern packaging, delivering a perfect, protective and attractive wrap every time, whether provided by a Automatic Shrink Wrapping Machine Supplier or a Semi Automatic Shrink Wrapping Machine Manufacturer.