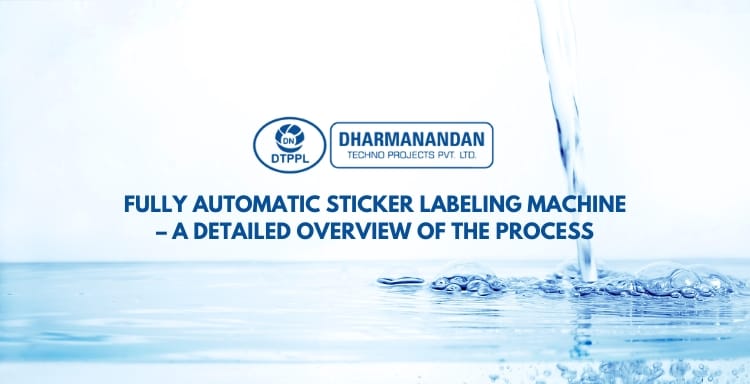
Table of Contents
Fully Automatic Sticker Labeling Machine – A Detailed Overview of the Process
February 5, 2025
1. What is an Automatic Sticker Labeler Machine?
In the world of packaging, branding, and product presentation, labeling plays a critical role. A well-placed sticker label not only enhances a product’s visual appeal but also provides essential information like branding, product details, barcodes, and regulatory compliance information.
For industries such as packaged drinking water and natural mineral water plants, food and beverages, pharmaceuticals, and cosmetics, the need for high-speed, precision-based labeling has led to the rise of fully automatic sticker labeling machines. These machines eliminate the inconsistencies of manual labeling, ensuring flawless application at high speeds, making them indispensable in modern manufacturing setups.
But what makes these machines so efficient? How do they work? And what factors contribute to their seamless operation? This article provides an in-depth exploration of their functionality, types, label materials, automation mechanisms, and the future of labeling technology.
2. Understanding Fully Automatic Sticker Labeling Machines
A fully automatic sticker labeling machine is an advanced packaging solution designed to automate the label application process. Unlike manual or semi-automatic systems, these machines require minimal human intervention, handling thousands of products per hour with extreme accuracy.
Key Components of a Sticker Labeling Machine
To understand how these machines work, let’s break down their core components:
- Label Roll Holder – Holds the roll of pre-printed or blank labels. The material feeds into the dispensing mechanism.
- Label Dispensing Mechanism – Peels off labels from the liner and applies them to products with precision.
- Sensors and Detection Systems – Identifies product position and ensures labels are correctly placed.
- Adhesive System – Ensures proper bonding between the label and the container or packaging.
- Conveyor System – Moves products through the labeling station at a controlled speed for consistent application.
- Control Panel (HMI – Human-Machine Interface) – Allows operators to set parameters, monitor performance, and troubleshoot errors.
These machines are commonly found in high-speed production lines, where speed and accuracy are crucial for large-scale manufacturing.
3. Types of Labeling Technologies Used
Different products and packaging types require different labeling techniques. Fully automatic sticker labeling machines offer a range of application methods, depending on product shape, label characteristics, and production speed requirements.
1. Wipe-On (Tamp-On) Labeling – The Classic Workhorse
One of the most commonly used techniques, wipe-on labeling, involves a direct, roller-based application of labels onto products.
How It Works:
- The machine feeds the label roll through the dispensing unit.
- A sensor detects the label’s leading edge and activates the peeling process.
- The label is peeled from its liner and applied onto the product using a roller or tamp pad.
- A final pressing mechanism ensures secure adhesion.
Pros:
- Simple and reliable, making it ideal for flat or slightly curved surfaces.
- Cost-effective and requires minimal maintenance.
Cons:
- Not suitable for high-speed operations.
- Struggles with complex or irregularly shaped products.
2. Blow-On Labeling – The Contactless Application
This method uses air pressure instead of physical contact, making it perfect for delicate or fragile items.
How It Works:
- The label is peeled off the liner and positioned above the product.
- A precise air jet propels the label onto the product’s surface.
- Electrostatic forces or adhesives help secure the label in place.
Pros:
- Ideal for irregularly shaped products or those that cannot withstand physical pressure.
- High-speed application suitable for fast production lines.
Cons:
- More complex and requires precise air pressure control.
- Higher initial investment compared to wipe-on labeling.
3. Wrap-Around Labeling – The 360° Embrace
Used mainly for bottles, cans, and cylindrical containers, this method wraps labels around the entire surface of a product.
How It Works:
- The product rotates as it moves along the conveyor system.
- The leading edge of the label adheres to the spinning product.
- As the product continues rotating, the label completes its full wrap-around.
Pros:
- Ideal for round bottles and beverage containers.
- Provides a 360° branding surface for maximum visibility.
Cons:
- Requires precise synchronization between label dispensing and product rotation.
4. Front and Back Labeling – The Dual-Sided Storyteller
For products that require both front and back labeling, such as food jars, cosmetics, and detergent bottles, this method applies two separate labels on opposite sides.
How It Works:
- Products pass through two labeling heads positioned on either side.
- Each head applies a label on the respective side simultaneously.
- The system ensures perfect alignment to maintain branding consistency.
Pros:
- Allows for different information on the front and back of a product.
- Works well with rectangular or oval-shaped containers.
Cons:
- More complex and requires precise alignment between the two labels.
5. Top and Bottom Labeling – Ensuring Full Coverage
This method is commonly used for trays, food packaging, and flat containers where branding or regulatory information needs to be visible on both the top and bottom surfaces.
How It Works:
- The top labeling head applies a label to the product’s upper surface.
- The bottom labeling head simultaneously applies a second label to the underside.
Pros:
- Useful for barcode placement and additional product information.
- Ideal for pre-packed foods, electronics, and consumer goods.
Cons:
- Requires dual synchronization to prevent label misalignment.
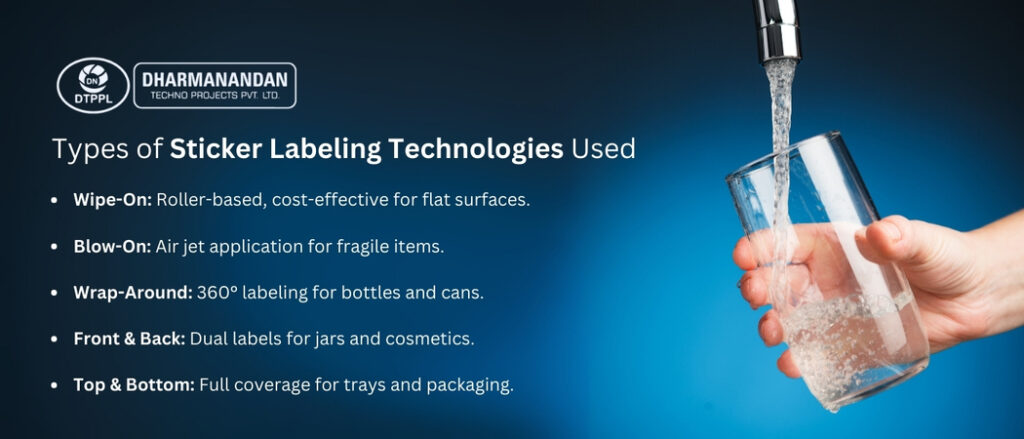
4. Sticker Label Materials and Adhesives
The quality of labeling depends not only on technology but also on label materials and adhesives. Let’s explore the different materials used in sticker labeling.
1. Facestock Materials (Label Surface)
The facestock is the top layer where printed text and graphics are displayed.
- Paper Labels: Cost-effective but prone to moisture damage.
- Polypropylene (PP): Water-resistant, commonly used for bottles and food packaging.
- Polyester (PET): High-strength, ideal for electronics and automotive labeling.
- Vinyl & Holographic Labels: Used for security and branding enhancements.
2. Adhesive Types (The Bonding Agent)
- Permanent Adhesives: Ensures strong, long-lasting adhesion.
- Removable Adhesives: Allows easy removal without residue.
- Freezer Adhesives: Designed for low-temperature environments like frozen foods.
- High-Temperature Adhesives: Used for heat-resistant applications.
3. Liner Materials (Backing Paper)
The liner holds the label before application.
- Paper Liners: Common in cost-effective applications.
- Film Liners: Used for high-speed dispensing, reducing waste.
5. Automation and Control Systems – The Brains Behind Automatic Sticker Labeler Machines
Automation is at the core of fully automatic sticker labeling machines, allowing them to operate continuously with minimal human intervention. These machines rely on advanced control systems, sensors, and actuators to ensure precision, efficiency, and consistency.
1. Label Dispensing Mechanism – Precision Peeling
The label dispensing mechanism is responsible for separating the label from its backing liner and applying it to the product at precisely the right speed and position.
- Peel Plate/Peeling Edge Design – The machine peels the label from the liner using a precisely designed edge that ensures a clean and smooth separation.
- Drive Roller System – A motorized roller pulls the liner forward, dispensing each label in perfect synchronization with the product’s movement.
2. Product Handling System – The Guiding Hand
For labels to be applied accurately, the product must be positioned correctly at the labeling station. This is achieved through:
- Conveyor Belt Dynamics – Products move along the conveyor belt, ensuring a steady flow through the machine.
- Star Wheel Indexing – A rotating star wheel holds and positions products precisely, ensuring accurate label application.
- Timing Screw Synchronization – Timing screws create consistent gaps between products, preventing misalignment during labeling.
3. Sensors – The Eyes and Ears of the System
Advanced sensors play a vital role in detecting products, aligning labels, and ensuring quality control.
- Product Detection Sensors – Identifies when a product arrives at the labeling station, triggering the label application process.
- Label Registration Sensors – Detects the edges of each label, ensuring it is applied in the correct position.
- Quality Control Sensors – Checks for misaligned or missing labels, preventing defective products from reaching customers.
4. Actuators – The Muscles of the Machine
The machine’s actuators provide the physical force needed to move components such as labeling heads, tamp pads, or air jets.
- Pneumatic Cylinders – Uses compressed air to press labels onto products, ensuring secure adhesion.
- Servo Motors – Provides high-precision movement, crucial for adjusting label positioning dynamically.
- Stepper Motors – Moves in small, controlled steps, ensuring exact label placement.
5. Control System (PLC) – The Central Nervous System
A Programmable Logic Controller (PLC) is the brain of the operation, ensuring that all components work in perfect synchronization.
- Receives input from sensors and triggers actuators to apply labels at the right moment.
- Allows customization for different label sizes, speeds, and adhesive strengths.
- Stores production data for quality control and traceability.
6. User Interface (HMI) – The Human Connection
The Human-Machine Interface (HMI) is how operators interact with the machine.
- Touchscreen Display – Offers an intuitive control panel for setting speeds, label sizes, and application parameters.
- Graphical Programming – Allows operators to customize labeling sequences easily.
- Remote Monitoring – Enables real-time tracking of machine performance, reducing downtime.
With these automated systems, fully automatic sticker labeling machines can operate at high speeds while maintaining exceptional accuracy.
6. Machine Configurations – Adapting to Different Production Needs
Different industries and production lines have unique requirements for labeling machines. Manufacturers offer various configurations to optimize efficiency and compatibility.
1. In-Line Labeling – Seamless Integration
In-line labeling machines are directly integrated into existing production lines.
- Products flow continuously on a conveyor, passing through the labeling station.
- Ideal for high-speed, high-volume production facilities.
- Easily synchronized with filling, capping, and packaging machines.
2. Rotary Labeling – High-Speed Efficiency
Rotary labeling machines are designed for extremely fast applications, handling thousands of products per hour.
- Products are fed onto a rotating turret, with multiple labeling stations working simultaneously.
- Perfect for bottling plants, beverage industries, and pharmaceuticals.
- Ensures high precision even at maximum speeds.
3. Standalone Labeling – Flexible and Versatile
Standalone machines operate independently and are often manually fed by operators.
- Used for short production runs or labeling customized products.
- Suitable for small businesses and laboratories.
- Can be moved between different production lines as needed.
These different configurations allow manufacturers to choose the best solution based on their production volume, product type, and budget.
7. Industries Using Fully Automatic Sticker Labeling Machines
A sticker labeling machine is used across a wide range of industries, ensuring brand consistency and compliance with labeling regulations.
1. Packaged Drinking Water and Natural Mineral Water Plants
- Labels convey brand identity, nutritional facts, and regulatory information.
- Wrap-around labeling is commonly used for bottled water and soft drinks.
2. Food & Beverage Industry
- Labels display ingredients, barcodes, expiry dates, and branding.
- Requires moisture-resistant labels for refrigerated and frozen products.
3. Pharmaceuticals & Cosmetics
- Labels provide dosage instructions, batch numbers, and safety warnings.
- Requires high-precision labeling to comply with strict industry regulations.
4. Automotive & Electronics
- Labels include serial numbers, barcodes, and part specifications.
- Adhesives must withstand heat, oil, and chemicals.
5. Logistics & Retail
- Used for price tags, shipping labels, and promotional stickers.
- Ensures barcodes are readable for automated scanning.
Each industry has unique labeling challenges, but fully automatic sticker labeling machines provide a customized, reliable solution.
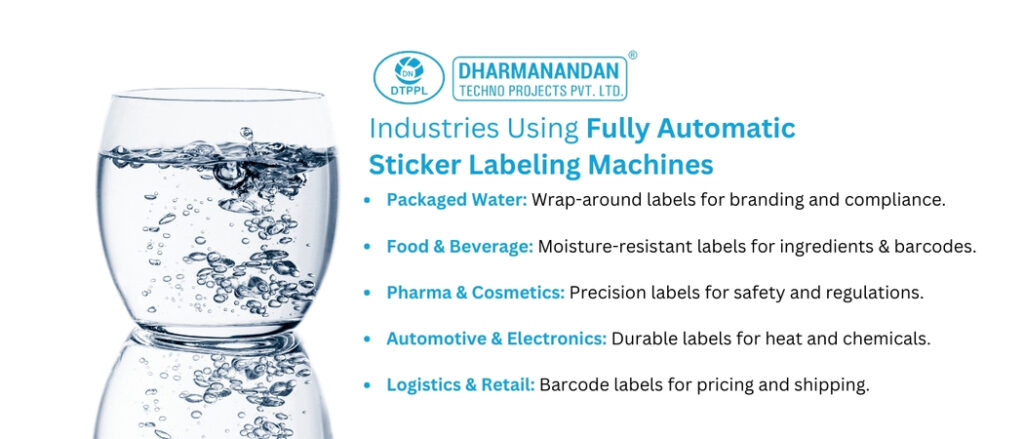
8. Benefits of Fully Automatic Sticker Labeler Machines
Investing in fully automatic sticker labeling machines brings several key advantages:
1. High Speed and Efficiency
- Capable of labeling thousands of products per hour, drastically reducing production time.
- Continuous operation ensures no bottlenecks in the packaging process.
2. Accuracy and Consistency
- Eliminates misaligned, wrinkled, or misplaced labels.
- Advanced sensors detect errors and adjust in real time.
3. Reduced Labor Costs
- Fully automated machines require minimal human supervision, reducing labor expenses.
- Employees can focus on higher-value tasks instead of manual labeling.
4. Improved Product Presentation
- Ensures professionally applied labels that enhance brand credibility.
- No bubbles, creases, or uneven placements.
5. Integration with Other Systems
- Can be integrated with filling, capping, and packaging machines for a seamless workflow.
- Allows for barcode scanning and data tracking.
6. Data Management and Traceability
- Records label data, batch numbers, and production history for quality control.
- Helps with product recalls and regulatory compliance.
9. Future Trends in Sticker Labeling Machines
The packaging industry is evolving rapidly, and sticker labeling machines are no exception. Manufacturers are investing in advanced automation, smart technologies, and sustainable solutions to enhance efficiency, accuracy, and eco-friendliness. Here are some of the key emerging trends shaping the future of fully automatic sticker labeling machines.
1. Smart Labeling & Industry 4.0 – The Age of Intelligent Automation
With the rise of Industry 4.0, sticker labeling machines are becoming smarter, more connected, and capable of real-time monitoring and automation.
RFID and NFC-Enabled Labels:
- Radio-Frequency Identification (RFID) and Near Field Communication (NFC) technology are being integrated into labels.
- These smart labels enable real-time product tracking, inventory management, and even interactive consumer engagement.
- For example, a customer can scan a NFC-enabled label using their smartphone to access product details, manufacturing information, or promotional offers.
Sensor Integration for Quality Control:
- Advanced sensors can now detect defective labels and automatically remove faulty products from the production line.
- Vision-based inspection systems ensure that each label is perfectly aligned and free from defects.
IIoT (Industrial Internet of Things) Connectivity:
- Labeling machines can be remotely monitored and controlled via cloud-based platforms.
- Manufacturers can analyze real-time data, predict maintenance needs, and reduce downtime by fixing issues before they escalate.
Cloud-Based Label Management:
- Companies are moving toward cloud storage for label designs, allowing seamless access from multiple production sites.
- This ensures consistency across global manufacturing plants and prevents errors caused by outdated label templates.
2. Automation & Robotics in Labeling – The Future of Precision Labeling
Traditional labeling systems are now incorporating robotics and AI-powered automation to increase precision and adaptability.
Robotic Labeling Arms:
- Unlike fixed labeling heads, robotic arms can adjust to different product shapes and sizes, making them ideal for irregularly shaped packages.
- They can rotate, tilt, and angle labels for perfect application, even on curved or uneven surfaces.
Vision-Guided Labeling Systems:
- High-speed cameras and AI-driven image processing help labelers identify product orientation and adjust label placement dynamically.
- This technology ensures flawless alignment, even if products are slightly mispositioned on the conveyor.
Collaborative Robots (Cobots) in Labeling:
- Cobots work alongside human operators, offering flexibility and easy programming for short production runs.
- These robots can be retrained quickly to handle different labeling tasks, making them perfect for custom or seasonal product labeling.
3. Sustainability in Labeling – Eco-Friendly Innovations
As global environmental concerns grow, industries are shifting toward sustainable packaging and labeling solutions.
Linerless Labeling Technology:
- Traditional labels require a silicone-coated backing liner, which contributes to waste generation.
- Linerless labels eliminate this waste, reducing material usage and disposal costs.
- This trend is gaining traction, especially in food and beverage, logistics, and retail industries.
Eco-Friendly Label Materials:
- Many manufacturers are switching to biodegradable and recyclable label materials such as:
- Sugarcane-based paper labels
- Compostable bioplastic labels
- Recycled PET (rPET) film labels
Water-Based Adhesives & Solvent-Free Labeling:
- Traditional adhesives contain solvents that release volatile organic compounds (VOCs) into the environment.
- The shift towards water-based adhesives reduces chemical emissions and carbon footprints.
4. Advanced Printing Technologies – The Evolution of Label Customization
Printing technology is playing a crucial role in making labels more dynamic and adaptable to market trends.
Digital Printing for On-Demand Labeling:
- Digital printers allow manufacturers to print labels in real-time, eliminating the need for large pre-printed label inventories.
- This is ideal for limited edition products, variable barcode printing, and personalized packaging.
Hybrid Printing Systems:
- Combines traditional flexographic printing with digital printing, offering the speed of conventional printing and the flexibility of digital customization.
- Allows for custom variable data (QR codes, serial numbers, promotional messages) while keeping mass production costs low.
5. Miniaturization & Modularity – Compact, Customizable Labeling Solutions
Compact Designs for Space-Saving Solutions:
- Newer labeling machines are designed to fit into compact production spaces, making them suitable for small to medium-sized enterprises (SMEs).
Modular Labeling Systems:
- Machines now feature interchangeable labeling heads, allowing businesses to switch between different labeling technologies without buying a new system.
- This enhances flexibility and scalability for manufacturers handling diverse product lines.
With these advancements, sticker labeling machines are becoming smarter, greener, and more adaptable, helping industries streamline operations while minimizing environmental impact.

10. Conclusion – The Future of Sticker Labeling Machines
Fully automatic sticker labeling machines are far more than just label applicators—they are the unsung heroes of product presentation, branding, and consumer engagement.
By ensuring precise label placement, high-speed application, and seamless integration with production lines, these machines enhance product visibility, regulatory compliance, and brand consistency.
With Industry 4.0 innovations, manufacturers are now leveraging smart labeling, robotics, and eco-friendly materials to make labeling processes more efficient and sustainable.
As technology continues to evolve, we can expect labeling machines to become even more advanced, offering real-time monitoring, AI-driven precision, and automated label adjustments to meet the dynamic demands of global markets.
Whether in packaged drinking water plants, pharmaceuticals, or the food industry, fully automatic sticker labeling machines will remain an indispensable asset, ensuring that every product is perfectly labeled, ready to capture consumer attention, and compliant with industry standards.